
Prof. Dr.-Ing. Robeller: „Reste aus Brettsperrholz sind zum Verbrennen viel zu schade"
Prof. Dr.-Ing. Robeller lehrt Digital Design and Production an der Technischen Hochschule in Augsburg mit dem Forschungsschwerpunkt Digitaler Holzbau. Bereits als Juniorprofessor an der TU Kaiserslautern (jetzt RPTU Kaiserslautern-Landau) forschte er an der Schnittstelle von Tragstrukturen, Ästhetik und Wiederverwendung im Holzbau. In diesem Rahmen entstand 2019 auch der DTC Hightech Holzpavillon in Diemerstein im Rahmen des Forschungsprojekts „Recycleshell“. Der Probebau wurde fast vollständig aus Resten von Brettsperrholzplatten (BSP) errichtet, die üblicherweise bei der Produktion von Fenster- und Türausschnitten anfallen. Mit Hilfe einer eigens entwickelten Planungssoftware (CAD-Plug-In) wurden der Materialeinsatz und der Verschnitt der Brettsperrholzplatten optimiert und daraus 200 individuell geformte Plattenelemente für den Pavillon automatisiert hergestellt.

Was ist das Forschungsprojekt „Recycleshell“? Was haben Sie damit erforscht?
Wir sind schon immer begeistert vom Prinzip Leichtbau, daher sind sogenannte „formaktive Tragwerke“ und Flächentragwerke eines unserer Spezialgebiete. Frei Otto, Meister des Leichtbaus und ein großes Vorbild für uns, hatte schon in den 1960er Jahren Holz als hochleistungsfähiges Baumaterial für solche Konstruktionen entdeckt. Die heutige Computer- und Robotik- Technologie eröffnet dabei nochmals ganz neue Möglichkeiten. In unserem Team fokussieren wir uns z.B. darauf, solche Tragwerke mit besonders nachhaltigem Holz zu realisieren, sei dies aus Abschnitten, aus weniger genutzten Holzarten, oder ohne den Einsatz von Klebstoffen.
Wie kann die Geometrie der Bauteile den Wareneinsatz und die Verschnittquote z.B. von BSP optimieren? Warum ist das wichtig?
Seit einigen Jahren ist Brettsperrholz ein sehr beliebter Baustoff, mit diversen Vor- und Nachteilen. Einer der Nachteile ist wohl, dass durch die Ausschnitte von großen Fenstern und Türen oftmals hohe Mengen an hochwertigen Abschnitten anfallen. Diese sind viel zu schade „für den Hacker“, also für die thermische Verwertung. Die geometrischen Daten der Abschnitte sind in aller Regel auch bereits erfasst, können also direkt weiter genutzt werden.

Es ist seit langem bekannt, dass bei der Produktion Ausschnitte von Brettsperrholz-Fenster- und Türelementen bis zu 25% des Materials als Verschnitt im „Müll" bzw. in der Verbrennung landen. Welche Ansätze sehen Sie in der Wiederverwendung? Gibt es verschiedene Methoden? Und welche Rolle spielt dabei die digitale Erfassung und Planung von Elementen?
Wir haben unter anderem gerade ein Paper veröffentlicht* in dem wir ein digitales Tool vorstellen, mit dem aus Abschnitten verschiedenster Geometrie wieder größere Wandelemente zusammengesetzt werden können. Dabei müssen diverse Aspekte berücksichtigt werden, unter anderem die Statik, Produktionstechnische Möglichkeiten, Anforderungen der Verbindungstechnik, Verschnittoptimierung. Wir sehen dies als spannende Aufgabe, gerade auch weil bereits viel leistungsfähige Technik in den Holzbaubetrieben vorhanden ist, oftmals mangelt es „nur“ an der Software. Die Entwicklung dieser bringt aber ebenfalls große Herausforderungen mit sich, vor allem entsprechend qualifizierte SoftwareentwicklerInnen zu gewinnen ist nicht einfach. Mit unserem neuen Technologietransferzentrum „Digitales Planen und Bauen“ können wir unseren MitarbeiterInnen nun einzigartige Forschungsmöglichkeiten bieten, inklusive der Promotionsmöglichkeit.
*Automated Panel Segmentation in CLT buildings using a multi-objective genetic algorithm, in SIGRADI 2024 International Conference Proceedings
Warum sind Nachhaltigkeit, Kreislaufeffektivität und Wiederverwendung im Bauwesen wichtig? Was sind die wichtigsten Erkenntnisse aus dem ersten Forschungsgebäude (DTC Hightech Holzpavillon)?
In den letzten Jahren ist sicher vielen Bürgerinnen und Bürgern bewusster geworden, dass es auch im Bereich des Bauens große Herausforderungen gibt. Nachwachsende Rohstoffe und Baustoffe spielen dabei sicher eine Schlüsselrolle. Wir dürfen dabei aber nicht nur auf die aktuelle Situation blicken, sondern müssen auch in die Zukunft schauen. Wie wird sich der Wald verändern, welche Baumarten und Holzprodukte werden in einigen Jahrzehnten verfügbar sein. Sowohl die Holzwirtschaft, als auch die Bauforschung brauchen lange Zeiträume, von den Ideen bis hin zur Umsetzung mit bauaufsichtlicher Zulassung. Daher ist gerade experimentelle Forschung mit Demonstrator Bauten so wichtig, um Erkenntnisse zu sammeln.
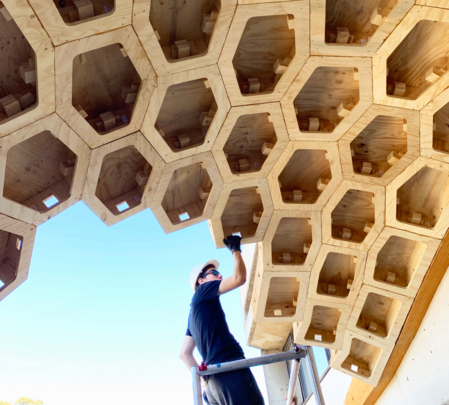
Sind auch komplexere Gebäude/Konstruktionen in der digitalen Entwurfsmethodik in Planung?
Unsere Forschungsgruppe untersucht viele verschiedene Anwendungsfälle, von den Sonderkonstruktionen und Flächentragwerken, bis hin zu ganz normalen Wandelementen. Komplexität kann dabei in jedem Anwendungsfall stecken, die spannende Frage ist eigentlich wo diese Komplexität sich befindet. Wir versuchen z.B. die Komplexität bei der Montage von Bauelementen so gering wie möglich zu halten, wohingegen die Komplexität innerhalb einer Software, eines Algorithmus der den Roboter steuert, gerne herausfordernd für uns sein darf.
Was bedeuten die Erkenntnisse des Forschungsvorhabens „Recycleshell“ für den Holzbau heute? Wie kann das Konzept bzw. die Software auf zukünftige Holzbauprojekte übertragen werden? Welche Vorteile ergeben sich daraus für die Wirtschaft?
Aus unserer Sicht ist es bei solchen Forschungsdemonstratoren immer wichtig, sich auf einige wenige experimentelle Neuerungen zu fokussieren. Während unsere geschätzten KollegInnen in Stuttgart kurz vorher erstmals eine sogenannten „trivalente Kuppel-Konstruktion“ aus Furniersperrholz (FSP)-Segmenten errichtet hatten (Landesgartenschau Schwäbisch Gmünd), war unsere Variante erstmals mit BSP-Segmenten realisiert worden. Dies erschien uns besonders interessant, weil gerade diese Abschnitte in großen Mengen anfallen. Zudem bietet das etwas dickere BSP mehr Spielraum für Verbindungen, wodurch wir erstmals in einer solchen Konstruktion komplett ohne Metallverbinder oder Schrauben ausgekommen sind. Stattdessen kamen bei uns innovative, CNC-ausgefräste X-Fix Verbinder komplett aus Holz zum Einsatz.

Welche Förderprogramme konnten Sie für die Forschung in Anspruch nehmen?
Wir sind bei diesem Projekt von verschiedenen Partnern unterstützt worden, allem voran das Umweltminsterium Rheinland-Pfalz, aber auch die Gemeinde Frankenstein / Diemerstein mit ihrem äußerst engagierten Bürgermeister, und ebenso sehr die Firma CLTech in Kaiserslautern und die Meisterschule für das Zimmererhandwerk Kaiserslautern, ohne welche dieses Projekt nie möglich gewesen wäre. Wir bedanken uns nochmals bei allen Unterstützerinnen und Unterstützern, u.a. Werner Theis, Hannsjörg Pohlmeyer, Eckhard Vogel, Jürgen Gottschall, Tobias Götz, Sepp Schilcher, Eva Saalfrank und Karl Jung.
Sie sind Professor an der Technischen Hochschule in Augsburg, waren zur Zeit des Forschungsprojekts Juniorprofessor an der TU Kaiserslautern. Wie wichtig für ist für Sie die Anpassung der Lehrinhalte hin zu mehr Zirkularität, Wiederverwendbarkeit und Nachhaltigkeit?
Ich bin in einem Handwerksbetrieb mit dem Werkstoff Holz aufgewachsen, und bis heute diesem Material sehr verbunden. Es ist ein besonderes Material, natürlich und individuell gewachsen, hochleistungsfähig aber auch äußerst komplex und anspruchsvoll. Selbst mit den vielen Jahren, die wir uns mit dem Thema beschäftigen, lernt man ständig neues dazu. Die Arbeit an einer Hochschule bietet die ideale Umgebung für ein lebenslanges Lernen und Lehren, mit vielen begeisterten KollegInnen, DoktorandInnen (wir haben seit 2024 Promotionsrecht) und Studierenden. Angesichts von Fachkräftemangel, Klimawandel und Materialknappheit sind wir von der Wichtigkeit dieser Forschung und Lehre überzeugt.